High-rise construction is a massive undertaking in every aspect. Through collaboration and careful decision-making, a team can establish a well-designed, coordinated, and successful process that can save both time and money. Clear coordination and careful planning, from the earliest stages of development, are critical factors for a smooth and successful build in what is usually a complex process involving different factors and many stakeholders.
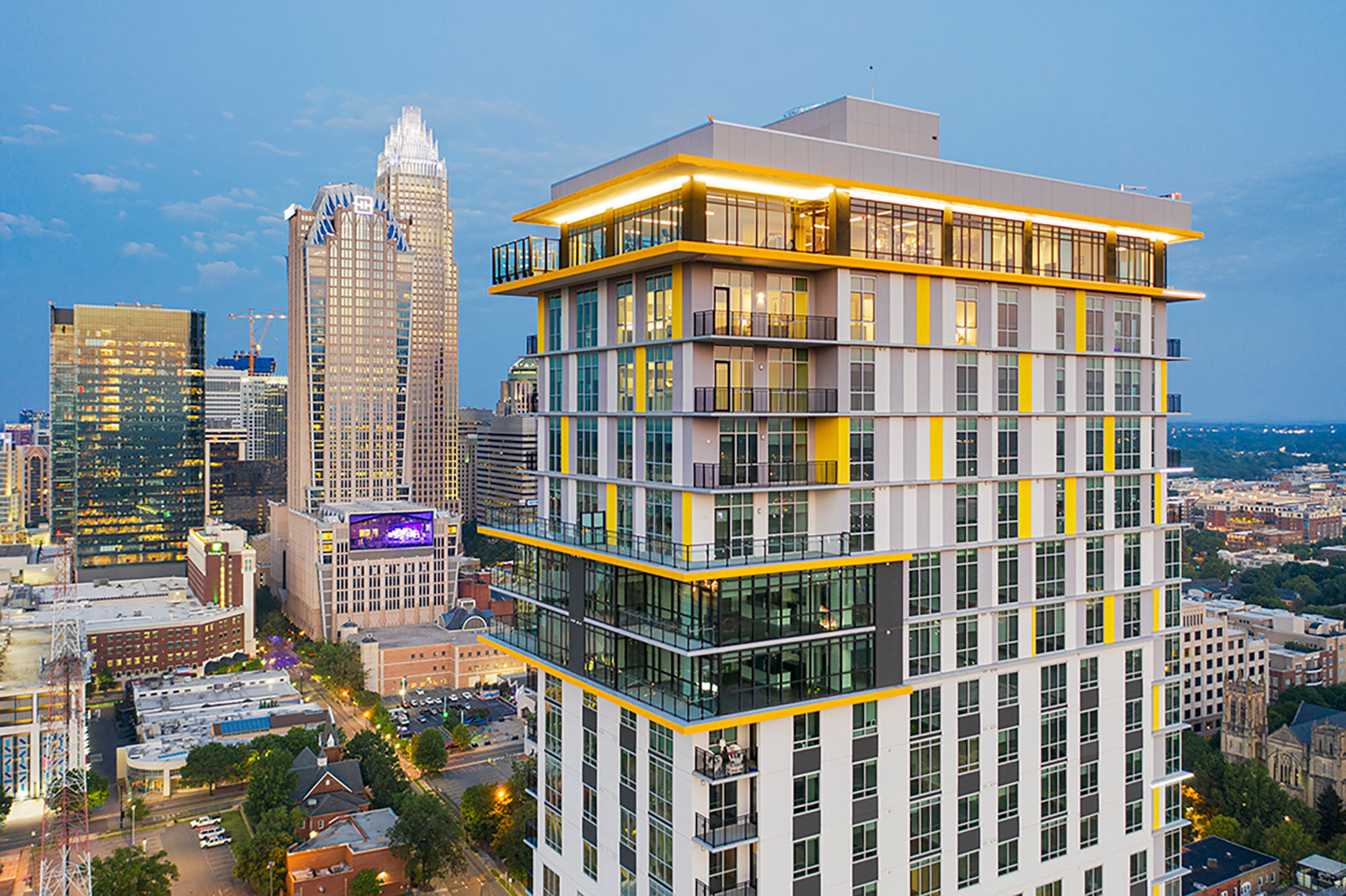
Residential high-rise The Ellis in Charlotte, North Carolina.
Structures at this scale require extensive forethought and consistent organization to keep the final product true to the design intent. This necessitates early interventions to avoid potential conflicts. Unit layouts offer a very good example of how these systems nest. If the design team wants to optimize the space for the best possible resident experience, it needs to consider construction documents (CD) details in their early discussions to facilitate that. As a hypothetical example: the placement of a mechanical closet in Unit A has ramifications for the position of the ductwork relative to the kitchen and the living room. It is not just about layout-it is about how the structure, the living space, and the mechanical infrastructure intersect. Time spent in discussing these details will have an exponential yield in saving time over the project’s lifetime.
To give a first-hand account of the impact of early level coordination on the life of a project, the following discussion will center around two different buildings: The Vermeer in Washington, D.C. and The Ellis in Charlotte, North Carolina. In this typology, everything starts early, from decisions on the mechanical systems, to alternative energy programs, to the location of the columns-they need to be locked down earlier. Decisions affect design, which affects decisions. An illustrative example of this kind of ripple effect comes from the author’s experience on working on The Ellis.
Design considerations for The Ellis
Selecting the building’s HVAC system early in the design process is important, as it will drive many design considerations moving forward. This article will review the design considerations and challenges that came after the team decided to move forward with split system heat pumps for the dwelling units early in the design process. This was a decision that brought cost benefits to the project, but also constructability challenges. The two main challenges were allocating the square footage to accommodate the required number of condensing units, and the line set not reaching 33 stories in length.
Line sets are copper piping that carry refrigerant from the outside condenser unit to the evaporator coil of the inside unit. There are maximum lengths for line sets depending on the unit and manufacturer, and this maximum length controls how far the exterior condensing unit can be from the interior system within the dwelling unit. Both vertical and horizontal distance must be factored in, and when the building is hundreds of meters (feet) in height, and has minimal roof area due to amenities for the residents, knowing that length is essential.
This is where collaboration, coordination, and creativity showed themselves in full strength. The team needed to use as much of the roof area as possible without compromising the rooftop pool deck, other outdoor amenities, and the iconic views this building offered. The challenges were not only the line set length of 33 stories, but also a lack of roof space that could accommodate condensing units for the upper half of the building.
For The Ellis, the two main challenges were allocating the square footage to accommodate the required number of condensing units, and the line set not reaching 33 stories in length.
Fitting the mechanical equipment
A structure of this height typically means a small footprint, high unit count, and limited space for mechanical units. There are many cases where an intermediate floor would be allocated solely for condensing units, as that would provide the additional square footage, easy maintenance access, and reach the portion of the building location the roof cannot accommodate. The downside is the potential for wasted net square footage that could provide future income.
Fortunately, in this project, the design team was able to take advantage of an adjacent eight-story pre-cast garage that services both the 33-story tower and the adjacent mid-rise building. An additional level was added to the garage to house most of the heat pumps and two large emergency generators. This added enough space for the condensers, but left the issue of line set length. In the end, for all the mechanical equipment to fit within the space available, and provide the necessary reach, variable refrigerant volumes (VRVs)—which are multi-split air conditioner system for commercial buildings—had to be installed in tandem with the split system heat pumps.
Structural engineering for a high-rise
Designing dwelling units is one of the early stages of design, which can have later ramifications, if done in a vacuum. During schematic design, the goal is to design and develop units that provide residents with an efficient, functional space, which they can also rent within the current market price. At this stage, the focus is not typically on structural elements.
Structural engineering is not yet engaged with the drawings and would usually around the design. This is fine for a wood frame building, where the structural walls create the spaces within the units, but in a high-rise, the structural engineer needs to be involved early. The structural engineer needs to review, analyze, and confirm the column placement, and provide feedback on the sizes and general column grid.
Columns within a concrete tower will heavily affect the layout of a residential dwelling unit, and not coordinating their locations simultaneously with the space planning of the units can be a hurdle.
Column coordination in The Vermeer
The Vermeer is a great example of the cascading effect of column coordination throughout a building. This particular project houses multiple uses within, multiple levels within each use, and every use has a different requirement when it comes to the spacing of columns.
The residential units need the columns to occur at the demising walls. Retail is best suited by columns in a perfectly square grid, spaced as far apart as possible, without touching the exterior storefront. The parking is best served by a perfect grid as well, but that grid is going to be different than retail’s ideal grid and, as an added complication, the site is not perfectly square. When these conditions in mind, sloping that one column near the closet entry door in unit plan A is no longer the biggest challenge.
Structural engineering and column design
Starting from the lowest level, parking should be designed as efficiently as possible since below-grade parking spaces are the most expensive type of space. Moving up to grade, retail is sandwiched between parking and the residential floors above-now the coordination process begins. At this point, the process can be complicated or creative, and it is frequently both. Retail levels typically occupy the most volume due to desired ceiling heights and this can be an advantage. Looking at an unframed concrete high-rise, a very literal view of how early decision-making impacts design can be seen. If it looks like the parking levels are on their perfect grid, one might notice how the columns shift and angle by the time the structure gets to the residential floors. Columns can step, slope, and they can also be transferred, and in the end, this project utilized every available technique to achieve its goals.
In the earliest stages, design teams and clients will be focused on unit plans and resident usability. However, it is crucial to give the structural engineer a seat at the same table when conceptualizing unit plans. This provides active feedback that considers column width, while the designers focus on the resident experience. Think of this as an ongoing conversation. If this process becomes siloed, then the designer might have to scrap a layout that has already been approved. To keep those finer touches intact, teams must have the structural engineer designing and calculating early on in schematic design. Livable, valuable units start with structural details such as column placement.
Coordination and communication
The process of coordinating, even between members of the same team, can be a challenge on projects such as The Vermeer and The Ellis. Keep in mind, there are consultants and contractors who also need to be aware of the design. There are many members of the design team today, especially on complex high-rise projects, but thanks to tools such as building information modeling (BIM) and more, the coordination process has taken on a new form over the years.
From sharing REVIT models to Navisworks clash detection, to live Bluebeam sessions, members of these large coordination teams can stay connected. It does not stop at the coordination between consultants, as the ability to have live PDF mark-ups has streamlined a more efficient way to exchange comments, thoughts, and solutions between the design team and clients. These tools keep teams and the project on track. Critically, they also keep the coordination conversation flexible and ongoing as decision-making shifts onto other details such as materials.
Constructability is another factor that should be part of the discussion from the beginning, to keep costs on track and the final product true to the original intent. Coordination between the design team and general contractors must be a priority during design development to make the most effective use of the expert construction knowledge available. Pushing these conversations to a later stage or leaving them until after breaking ground causes construction delays and on-the-fly solutions. Getting the general contractors to the table early and often to provide essential feedback on cost, availability, and constructability is essential to an efficient design process and to success later in construction. Without this coordination, details may require redesign due to site conditions, costs, or construction.
Selecting the right materials
There are many different materials and construction systems to choose when building a high rise—each with its upfront and hidden costs and benefits. Steel and concrete are traditional choices, with light gage steel becoming a more attractive option. It is important to consider the construction and delivery methods early on. Will there be panelized or modular components? If so, how will the team coordinate with the factory to get them delivered on time? Where will the materials be stored when the building is under construction? The question then becomes figuring out if the right choice has been made and then how to move forward in this process.
In working on The Vermeer, the author’s firm had an ongoing early-stage discussion of light gage steel versus concrete. It started by looking at the height, footprint, and overall massing of the building. Both materials suited the general design intent, but the relevant question was, which one is the most efficient way and has the fewest compromises?
Once wood framing is out of the picture, only a few other structural options remain, and light gage is one of them. For The Vermeer, the height of the building was an important consideration. Would it get to the point where the lower levels would require steel to pick up the loads coming from above? The footprint and massing also had to be considered; would there be a lot of acute corners, are there multiple step backs and cantilevers? The answer to both questions is yes. Does the program include that top of the market rooftop amenity with a pool? What mechanical system is being utilized? All these elements need to be reviewed in depth and considered when making the decision of the structural system of the building.
The Vermeer is 12 stories, plus penthouse amenities; it contains multiple acute angles due to the site constraints, multiple stepbacks at the top floors due to zoning requirements, an extensive green roof to adhere to the energy code, and rooftop amenities and pool as the site offers 360-degree views. Considering all the above, the design team made the decision to move forward with a concrete structure. This allowed the design to thrive and to take advantage of zoning-required step backs, to get creative with the site’s acute angles, to push the limits on the extent of the green roof and move forward on what will be another addition to the iconic skyline.
The Vermeer is 12 stories and features penthouse amenities. It contains multiple acute angles due to the site constraints, multiple stepbacks at the top floors due to zoning requirements, and an extensive green roof to adhere to the energy code.
The sustainability aspect
It is common to think of sustainable building measures as entirely separate from cost, communication, and constructability concerns. Green building design, however, can be a cost-effective choice, and can lead to a well-planned project that runs on time with a highly coordinated team, and leads to less waste as well.
Choosing sustainable materials early in the process and coordinating with construction experts to select construction techniques that make a high-rise both more sustainable and constructable (e.g. modular and panelized construction), lead to a more efficient build in every respect. In thinking about sustainability, it is important to take a high level approach. A sustainable building is more than just solar panels and renewable materials. Longer build times mean more fossil fuels, and bad communication can mean those sustainable materials do not make it to the site on time. Effective early decision making is as important to the bottom line for both a monetary and a carbon budget.
The design team and ergonomics
The ergonomics of a building are what drives the design throughout the process. Each decision made, from the column placement to the type of heating, (e.g. gas or electric), to window placement, and even the selection of light fixtures can make or break the final residential experience.
Ultimately, design teams want the functionality and movement through the building to be as efficient as possible, and for it to resemble the efficiency they find in the chosen materials and building systems. If design teams are not asking themselves “How will this affect the resident?” prior to making a decision, then there is a high likelihood that final experience will be compromised.
Often, teams spend a lot of time focusing on the exciting areas of the building when thinking about the end user experience and the renter. However, they should not overlook some of the major components to the ergonomics of the building that are not as flashy or glamorous.
Consider two back-of-house areas: loading and trash. No one wants money spent here, but if these areas do not function at a high level, it can throw off the entire project; especially for the residents. These may seem like simple spaces to account for, but the coordination effort that need to go into these spaces is extremely high. To start, consider height clearances. Does zoning require a specific height? Does the height align with the proposed moving, delivery, and trash trucks that will service the project? What is the structure, and does it require any deeper beams or thicker slabs in order to span the large open space that trucks require to turn around and move throughout?
When looking at all these factors, the decisions made can start to ripple up the building. If the columns are shifted for the trucks, how does it affect the unit above? If a beam is added to increase the span, how does it affect the plumbing coming down from the above unit? If the trash compactor is moved to function better with the truck movements, how does it affect the access rooms above for the residents and does it modify a unit layout? The back-of-house functional spaces can significantly affect the coordination for the overall ergonomics of the building, which in turn, drive the residential experience.
Conclusion
Design teams can select the right materials and design around them, they can think about modularity and panels, but it must culminate in a place where people want to live-a place people will call home. Design efficiency is important, end user experience is important, but finding that median, the balance between the two, is the key to a great final product. It is vital to have these conversations as early as possible, avoid the surprises, not compromise resident experience due to lack of resources and rushed decisions, and above all, coordinate with everyone involved.
Key Takeaways
The construction of a high-rise building is a complex process that requires careful planning, coordination, and collaboration among different organizations and stakeholders to ensure a smooth and successful build. In this article, two different high-rise buildings, The Vermeer in Washington, D.C., and The Ellis in Charlotte, N.C., are used as case studies to illustrate how early level coordination can impact the life of a project. One of the challenges the Ellis team faced was allocating square footage to accommodate the required number of condensing units and ensuring the line set lengths did not reach 33 stories in length. Collaboration, coordination, and creativity were utilized to overcome this challenge, and an adjacent eight-story pre-cast garage was used to house most of the heat pumps and two large emergency generators. In addition, coordination and planning were also necessary in the design of the dwelling units, as the placement of columns within a concrete tower can heavily affect the layout of a residential dwelling unit. The article emphasizes that clear coordination and careful planning from the earliest stages of development are critical factors to a smooth and successful build.